7 min read
The Importance of Effective Operating Procedures
By: Innovatia on Oct 2, 2020 11:17:06 AM
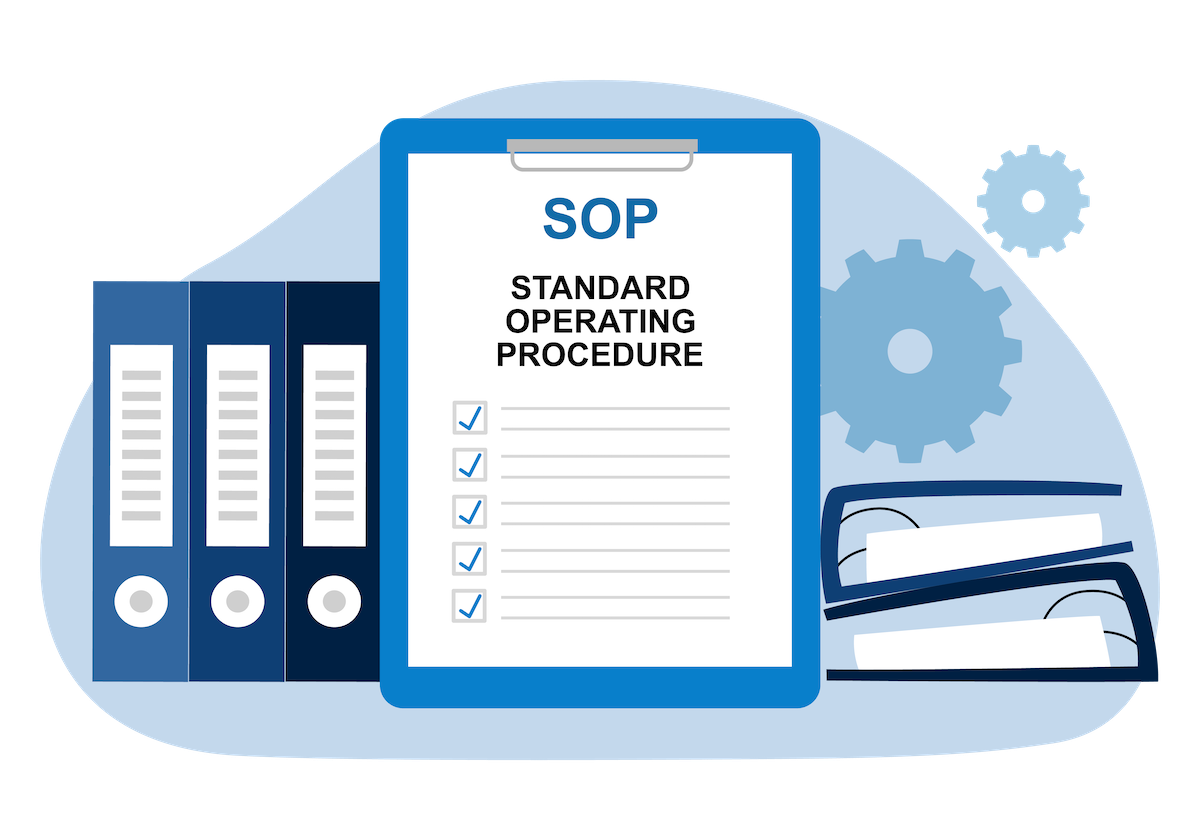
Operating procedures are step-by-step instructions detailing how to perform specific tasks, such as starting up or shutting off equipment, responding to incidents, or completing maintenance. These procedures are not limited to routine tasks but include emergency response, maintenance, and troubleshooting. While most organizations have some form of operating procedures in place, their effectiveness often varies. Effective operating procedures can significantly impact safety, efficiency, and compliance, making them essential for modern businesses.
The creation of effective procedures often involves professional technical writing services and documentation services, ensuring accuracy and clarity. Organizations can streamline procedure development and maintenance by utilizing content automation and structured content approaches.
Characteristics of Effective Operating Procedures
Effective operating procedures share common traits that ensure their usability and reliability:
-
Correct: They accurately describe the proper steps to accomplish a task.
-
Clear: They use straightforward language that is easy to understand.
-
Comprehensive: They cover all necessary information, including handling unexpected scenarios.
-
Communicated: Training provides steps on how to use the procedures effectively.
-
Accessible: Procedures are easy to locate, especially in emergencies.
-
Maintained: Documentation is reviewed regularly and updated to reflect current best practices.
Organizations can rely on content governance, content workflows, and enterprise content management systems to achieve these characteristics.
The Importance of Effective Operating Procedures
Safety
Safety is paramount in industries such as energy, engineering, and manufacturing. Effective procedures help mitigate risks by clearly outlining necessary precautions, required safety equipment, and steps to avoid hazards.
When emergencies occur, clear procedures enable operators to respond promptly and accurately. According to the Abnormal Situation Management (ASM) Consortium, more than half of inadequate responses to abnormal situations stem from poorly executed procedures. This highlights the importance of process improvement and knowledge management systems in procedure development.
Efficiency
Efficiency directly impacts an organization’s bottom line. Clear and concise procedures eliminate unnecessary steps, reduce errors, and ensure tasks are completed right the first time. They also improve productivity during routine operations and help avoid disruptive activities like plant shutdowns.
The use of enterprise content strategy and content optimization tools ensures that procedures are both efficient and user-friendly, which also supports faster onboarding of new employees.
Building Safety Through Procedures
Safety-oriented operating procedures depend on practical competency-based training and training solutions. Regular training sessions ensure operators understand and follow the procedures correctly. Additionally, engaging e-learning tools and enterprise learning solutions can enhance safety training programs.
Driving Efficiency with Clear Procedures
Efficient operating procedures incorporate structured content to eliminate redundancies and streamline workflows. For example, using content automation to update multiple documents simultaneously ensures consistency and saves time. Experienced operators can also provide feedback to improve established procedures, leveraging organizational knowledge management practices.
Assessing your Procedures
Organizations can evaluate their procedures by answering the following questions:
1. Are all operational procedures documented, including emergency response and maintenance tasks?
2. Are the procedures clear and task-oriented?
3. Are they easily accessible in emergencies?
4. Are they regularly reviewed and updated?
5. Do operators receive training on procedure use and updates?
6. Is there a process for operators to provide feedback and flag issues?
If the answer to any of these questions is “no,” it may be time to adopt a holistic approach to content lifecycle and documentation management.
The Role of Technology in Operating Procedures
Technology plays a vital role in modernizing operating procedures. Content creation processes powered by AI can reduce manual effort, while e-learning platforms enhance training. By adopting enterprise learning solutions, businesses can foster a culture of continuous improvement.
How Innovatia Can Help
Innovatia specializes in providing end-to-end solutions for effective content management including operating procedure documentation. From content strategy and instructional design to technical documentation and user experience content, Innovatia offers the expertise and tools to optimize your operations. Whether enhancing safety or boosting efficiency, assess your procedures today and discover how Innovatia can support your journey toward streamlined and effective operations.
ABOUT INNOVATIA
Innovatia is an end-to-end content solutions provider servicing clients looking to manage and overcome challenges with their content. For more than two decades, our experts have worked closely with client teams to help design, transform, and manage their content with a view to driving business goals through knowledge and content solutions. To discuss in more detail, contact us.
Related Posts
Improving Customer Service Consistency
Delivering a consistent experience to your customer is an essential requirement for any business....
Organizational Knowledge Management: Take it one step at a time
The first step to closing the gaps is to acknowledge that they exist. Streamline your...
The Role of Technical Writer and Content Architect
Technical writers, remember creating standalone deliverables? —print manuals, CHM files,...